The Genelec 8361A studio monitor is the company’s flagship product – this is how we made it
The quality of Genelec’s speakers comes from perseverance, continuous improvement, and healthy and happy employees. All of the products made by this audio pioneer are designed and manufactured at the company’s factory in Iisalmi, Finland.
Clear goals and perseverance lay the foundations for high-quality operations. The Iisalmi-based speaker manufacturer Genelec has had a clear mission ever since the company was established in 1978.
“We want to make the world’s best audio solutions for professionals. This is why the company exists,” says CEO Siamäk Naghian.
The company’s story began in 1976 when two postgraduate acoustics students, Ilpo Martikainen and Topi Partanen, heard that the Finnish Broadcasting Company Yle needed active speakers to monitor sound quality in its newly built broadcasting house.
A prototype speaker was completed only a couple of weeks later, and Yle was interested. The principle behind an active speaker is that each frequency range has its own amplifier and all of the electronics are built into the speaker.
Genelec speakers aim to reproduce sound as faithfully as possible without adding or removing anything. The company’s first active speaker model, the S30, was introduced in 1978.
“Genelec has been making long-lasting products from the outset. The best thing in terms of sustainable development is that a speaker made 46 years ago is still in use and serviceable,” says Naghian.
In this video, Genelec’s employees and CEO talk about the company’s culture.
MEANINGFUL WORK
Quality is the sum of many factors, and forms the basis of Genelec’s corporate culture. You need good leadership, skilled employees, and continuous and systematic development and steering.
“Expertise and wellbeing of the emloyees are basic requirements for quality. Things are in good shape when we feel that we’re doing meaningful work while also having the opportunity to develop and move forward,” says Naghian.
Genelec’s first decade was a struggle for existence. The turning point came in 1989, when the 1035A was demonstrated in London and became the benchmark for studio monitors. This model was described as having the loudest sound and least distortion of any speaker on the market.
Expertise and wellbeing of the emloyees are basic requirements for quality.
Over the years, Genelec has introduced speakers with new technical features, designs and materials that have changed the industry. Rounded shapes, die-cast aluminium housings and calibration technology that automatically adjusts to the acoustic environment are just some examples of Genelec’s Research and Development.
Even today, all Genelec speakers are developed and manufactured at the company’s Iisalmi factory on the shores of Lake Porovesi in Upper Savonia.
“We see manufacture and product development as one. Which is why we’ve never considered making our products anywhere else,” says Naghian.
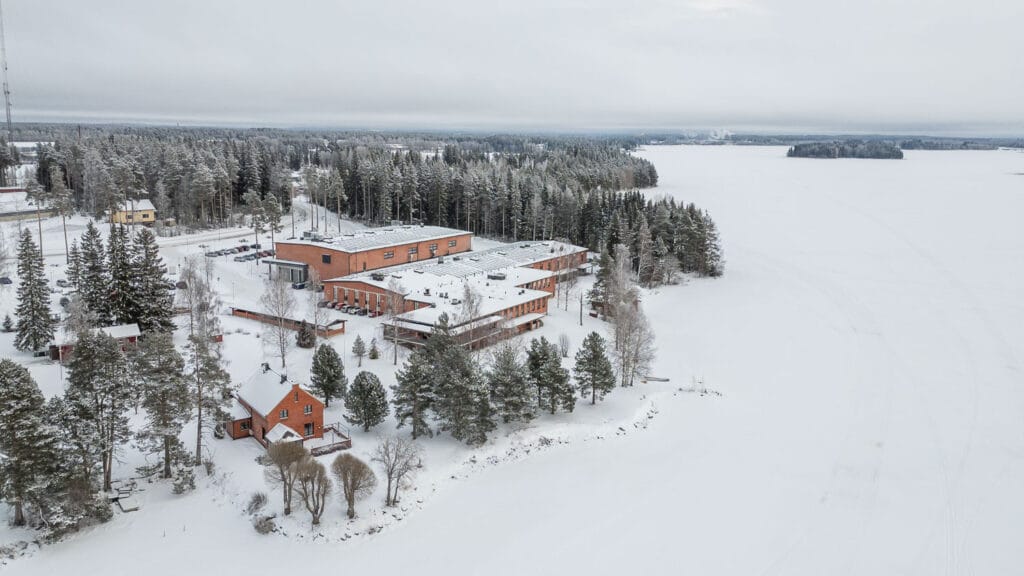
ALL PRODUCTS TESTED
Genelec manufactures its own circuit boards and other key components to ensure that quality requirements are met.
“Electronics manufacturing is important to us. Each speaker has at least one circuit board,” says Piia-Riitta Bergman, Chief Operational Officer.
All of Genelec’s self-manufactured components and finished speakers are tested.
“The basic process is the same regardless of the model. Each product is tested individually before being sent to the customer,” says Bergman.
We encourage people to voice their ideas, so that we can work on them together.
Genelec has a broad range of models. Sales volumes vary, and new models are released on a regular basis. Its business revolves around lifelong learning and multiple skills.
“It’s great that we have so many people who are able to do a variety of production tasks,” says Bergman.
At Genelec, it is standard practice to give everyone the opportunity to learn and develop. Good ideas are requested – and also implemented.
“We seek suggested improvements from both teams and individuals. We encourage people to voice their ideas, so that we can work on them together,” says Bergman.
RESPONSIBILITY AND MOTIVATION
Vesa Pelkonen, the chief shop steward for production personnel, says that employees are genuinely involved in design and development at Genelec.
“Almost all proposals have gone through, as long as they’ve been justified. We’ve had no problems with our employer. Conversations take place in good faith,” says Pelkonen.
Long-term employment is one of Genelec’s guarantees of high quality. Experience helps when accuracy is required. And accuracy is also reflected in people’s wallets.
“The quality of a delivery affects our pay. It also motivates us to focus on quality,” says Pelkonen.
We’ve had no problems with our employer. Conversations take place in good faith.
At Genelec, the assembly of large speakers in particular is usually in the hands of just one person – all the way down to checking and packaging the speaker.
“I’ll make a speaker from start to finish, and I’ll also be the last one to check it. It’s my responsibility,” says Pelkonen, who works in assembly.
GENELEC 8361A
The largest studio monitor in The Ones range
Die-cast, powder-coated aluminium housing
Amplifiers: 700W bass, 150W midrange, 150W treble
Frequency response: 30 Hz – 43 kHz
Maximum sound pressure level: 118 decibels
Dimensions: 593 x 357 x 347 mm
Weight: 31.9 kg
Price: about EUR 5,000
This is how we made it
1 ELECTRONICS TECHNICIAN ARTO LÄMSÄ monitors the machine that assembles components such as circuits, coils, resistors and capacitors during the manufacture of printed circuit boards. The machine will detect when a component is misaligned or reversed, and the assembly will then have to be manually corrected. After assembly, the circuit boards are placed into a reflow oven to solder the components into place. The internal temperature of the circuit boards is kept at a steady 22 degrees Celsius with a moisture percentage of 40 per cent to ensure correctly soldered joints.
“It’s pleasant in here during the winter in particular, when it’s dry outside. Your skin gets to absorb some moisture indoors,” says Lämsä.
Having multiple skills brings some variety to the job.
“I also do manual assembly and soldering. It keeps you sharp and stops your mind from rusting.”
Lämsä has been working at Genelec for 18 years. His work has changed a lot during that time.
“We used to clamber up the shelves and do all sorts of stuff. But occupational safety is in good shape these days. It’s a miracle that nothing bad happened back then,” says Lämsä.
2 PRODUCTION SPECIALIST MIRVA HOLOPAINEN manually assembles components onto printed circuit boards. Through-hole components are mounted onto the circuit board from below in a wave soldering machine. Before the speakers are assembled, all of the completed circuit boards are visually inspected and tested to make sure they work.
Holopainen has been at Genelec for 23 years, during which time she’s worked in circuit board manufacture, assembly and the café.
Holopainen has been a production specialist since 2021. Her current job description includes not only circuit board manufacture but also work study and onboarding new recruits. Work study involves carrying out a variety of time and observational studies and developing working methods.
“Genelec is an excellent employer. Our work is varied and interesting, and we also have the chance to advance our careers on the basis of our own interests,” says Holopainen.
High-quality speakers are the result of teamwork.
“Producing high-quality speakers for our customers gives us a sense of professional pride. Satisfied customers are close to our hearts,” says Holopainen.
3 ELECTRONICS TECHNICIAN TIIA KOMULAINEN makes speaker components that are tested before the speakers are assembled.
Komulainen has been working at Genelec for three years and has enjoyed the variety in her job.
“This is a really great place to work. My work is quite varied, as we manufacture a variety of different models,” says Komulainen.
Employees also have a say in both their own work and how the unit operates. Research and development adds to the interest.
“Everyone is familiar with all of the models. We get to have a say in what we do. Everybody has their own favourite models,” says Komulainen.
4 LOGISTICS TECHNICIAN VEIJO TOSSAVAINEN gathers ordered components from the inventory and places them onto the cart for assembly. In order to minimise the potential for error, only the components specified in the order will be placed on the cart. Tossavainen has been working at Genelec for 24 years.
5 ELECTRONICS TECHNICIAN JANNE HAKALA places the two halves of the speaker’s die-cast and powder-coated aluminium housing into the plastic frame in which assembly takes place. The circuit boards, speaker components and other components are screwed into place. A barcode label is printed for the speaker, and the barcodes on the speaker components are read so that both the components and manufacturing process can be traced later on. Finally, Hakala screws the two halves of the speaker housing together and uses a leak test device to test its tightness. This type of speaker is built from start to finish by one person.
“I’ve always been interested in acoustics and speakers. It’s great when you also get to do your hobby at work,” says Hakala.
Hakala, who has been with Genelec for four years, says that he has mainly focused on assembly tasks. Variety comes in the form of different speaker models.
Hakala also has Genelec speakers at home.
“They let you hear the sound as the musicians and filmmakers would have wanted it,” says Hakala.
It’s rewarding to make products that are recognised for their high quality all across the world.
“We make these speakers with pride. It even creates a little bit of pressure, when you know that the quality of your products has to be the absolute best,” Hakala says.
6 The finished speakers are loaded onto a cart and sent to a chamber whose acoustics are designed for final testing. The tests will be carried out by the same person who assembled the speaker. Initial tests ensure electrical safety. The software then calibrates the speaker to the desired values. The tester makes sure that no air is leaking from the seams, by both feel and listening. Finally, an audio sweep across the entire frequency range is played through the speaker, while the tester conducts a by-ear audio test to make sure that nothing extra is being added to the sound.
“The sound is faithfully reproduced. Our speakers don’t colour the playback,” says Janne Hakala.
All testers must pass a training course in which they learn to detect a variety of faulty sounds.
“During the training, people listen to bad speakers and identify what’s wrong with them,” says Hakala.
7 The same technician who assembled and tested the speaker will also pack the finished product. The suction cups on the lifting apparatus stick to the sides of the speaker, so that even a product weighing more than 30 kilos slips easily into the cardboard box – along with a manual. Finally, the package is stapled closed. When the order is complete, a logistics employee collects the products and delivers them to the customer.
“There’s nothing we can’t talk about”
Continuous collaboration between departments and teams has proven to be an effective model at Genelec. Openness builds trust.
Genelec was also tested by the international financial crisis in 2008. CEO Siamäk Naghian says that good things also came out of the crisis.
Codetermination negotiations were held within the company as a result of the economic downturn, but this also opened the door for continuous and active collaboration involving everyone.
“We’re improving our operations together and have rediscovered the key role of codetermination negotiations. And in my job, they’re at least as important as the management team,” Naghian says.
The company will grow, but I think the most important thing is to preserve our identity and philosophy.
Chief shop steward Vesa Pelkonen says that continuous cooperation and openness create a culture of trust. The company’s internal matters are discussed together – with trust and confidence.
“Every other Monday morning, we have a briefing at which our employer keeps us informed about current issues. Nothing is kept secret,” says Pelkonen.
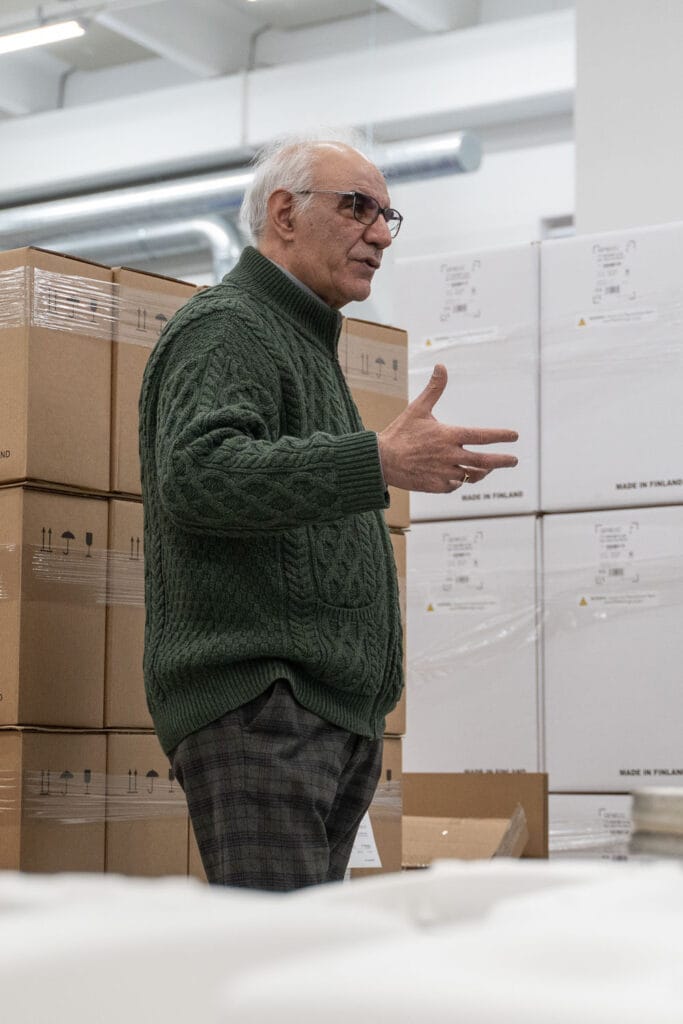
A FORERUNNER IN THE FUTURE TOO
Openness helps to ensure that issues don’t spread as rumours and nothing comes as a surprise. This enables the company to adapt to changing situations.
“Everyone is kept up to date. There’s nothing we can’t talk about,” says Naghian.
The future looks bright at Genelec. This second-generation family business continues to be a forerunner in its industry.
“The company will grow, but I think the most important thing is to preserve our identity and philosophy. It’s beautiful,” says Naghian.
GENELEC OY
ESTABLISHED 1978
DOMICILE Iisalmi
MANUFACTURES Audio systems for audio professionals, installations and home listeners
PERSONNEL About 210 (Group 270) of which about 100 work in production
OWNERSHIP Juho, Maria and Mikko Martikainen, Topi Partanen and Ritva Leinonen.
NET SALES EUR 38.4 million, Group about EUR 50 million (2023)
Read the article in Finnish: Genelec 8361A studiomonitori on yrityksen lippulaivatuote – näin sen teimme